Onderdelen uit 3D-printer? Dit kan met 3D-printtechniek
De 3D-printtechniek ontwikkelt zich snel. Inmiddels doet 3D-printen zijn intrede in de landbouw. Er kan al veel en er kan ook steeds meer. TREKKER bezoekt twee pioniers in de 3D-printtechniek.
Een rij witte kasten met een beeldscherm en een raam met blauw licht dat er uitziet als een magnetron. Geen mannen in witte pakken, dat nog net niet, maar je waant je in een medisch laboratorium of een chipmachinefabriek. We zijn bij K3D in Terborg (Gld.). Het bedrijf is gespecialiseerd in metaal printen. Stijn Luttikholt, ontwerpspecialist van K3D, doet uit de doeken hoe de 3D-printtechniek werkt, wat er kan en wat er niet kan.
Het principe van de 3D-printtechniek is eenvoudig: je laadt een driedimensionale tekening in de computer, waarna die het werk voorbereidt. Vervolgens druk je op de knop en de printer gaat aan de slag. Een paar uur of een paar dagen later – afhankelijk van de grootte van het object en onder andere de gekozen laagdikte van het printen – is het onderdeel klaar. Al voor een paar honderd euro koopt een hobbyist een kunststofprinter voor beginners. Voor een paar duizend euro staat er een redelijk professionele machine.
Metaal printen gaat min of meer volgens hetzelfde principe. In detail vergt het toch een heel andere techniek, en daardoor ook een heel andere investering. Om kwalitatief hoogwaardige onderdelen in metaal te printen gaat het om een investering van zeven cijfers voor de komma. Daarbij vergt het de nodige kennis en ervaring om tot een goed resultaat te komen.
Tekst gaat verder onder de foto
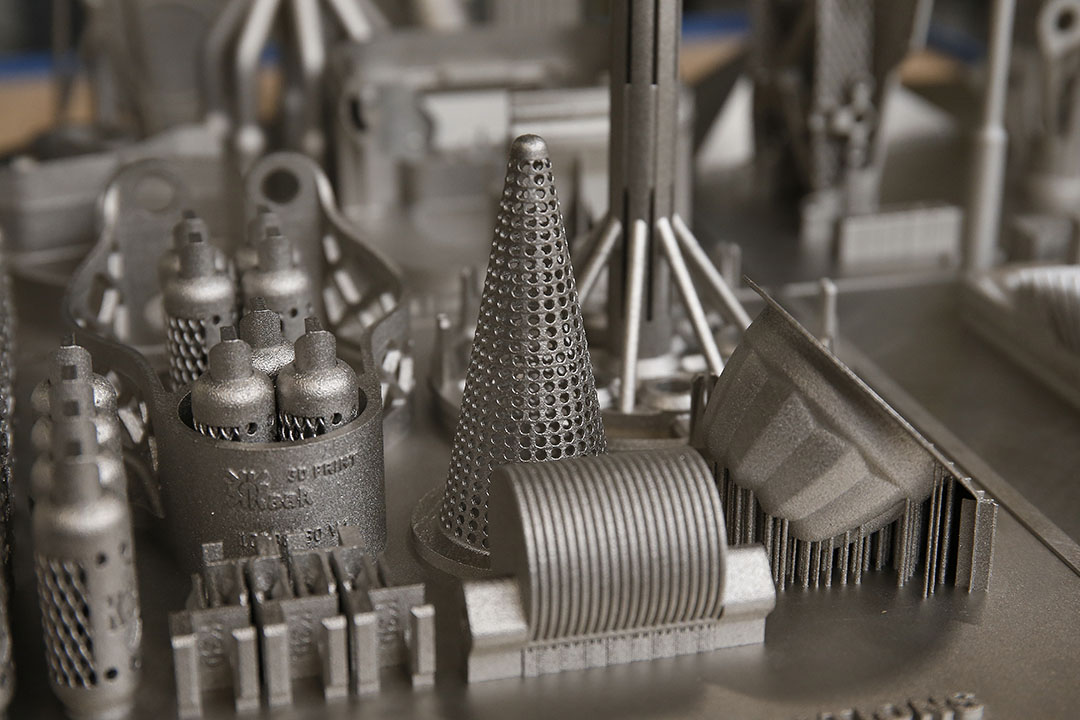
3D-printen gaat vaak met meerdere onderdelen tegelijk. Dat kunnen de meest bizarre vormen zijn. Het 3D-printproces neemt vaak meerdere dagen in beslag.
Metaalpoeder als basismateriaal
De metaalprinters van K3D gebruiken metaalpoeder als basismateriaal. Dat kan metaal van verschillende legeringen zijn. Elk type legering heeft een eigen, gescheiden printkamer om vermenging van metaalpoeders te voorkomen. K3D kan vier soorten metaal printen:
-
rvs 316L (voedingsmiddelenindustrie)
-
aluminium (AlSi10Mg) voor bijvoorbeeld warmtewisselaars
-
gereedschapstaal 1.2709
-
titanium Ti6Al4V voor bijvoorbeeld medische applicaties
Een voorbeeld van kunststofprinttechniek is het aanvoeren van een draad die versmolten wordt om producten laagsgewijs op te bouwen. De metaalprinter versmelt een laag metaalpoeder met een laser tot een massief materiaal in een inerte printkamer (maximaal 0,05% zuurstof aanwezig).
Het proces is als het ware het constant aan elkaar lassen van metaalpoeder. De warmte om te lassen komt bij een poederprinter van de laserstralen. De laser zelf beweegt niet. Een stelsel van bewegende spiegels bepaalt exact waar de laserstraal komt en het poeder tot een geheel last.
Powder Bed Fusion (PBF) is de officiële naam van deze techniek. De printlagen zijn 30 tot 60 micron dik (0,03 tot 0,06 millimeter) en de machine kan diktes vanaf 0,11 millimeter printen. De printlaagdikte hangt af van het gewenste materiaal en de toepassing of wensen van de klant. Vanwege sterkte en printbaarheid is het advies een minimale wanddikte van 0,5 millimeter.
Nieuwe techniek: versmelten lasdraad
Een nieuwe techniek waarmee K3D is gestart, is het versmelten van lasdraad dat automatisch wordt aangevoerd door een robot. Het printbereik is hierdoor veel groter dan bij een poederprinter. Je kunt dan ook grotere onderdelen maken, en het werkt ook sneller. In een aparte printruimte stapelt de robot geduldig de lasrupsjes op elkaar, en maakt zo de meest uiteenlopende vormen.
Tekst gaat verder onder de foto
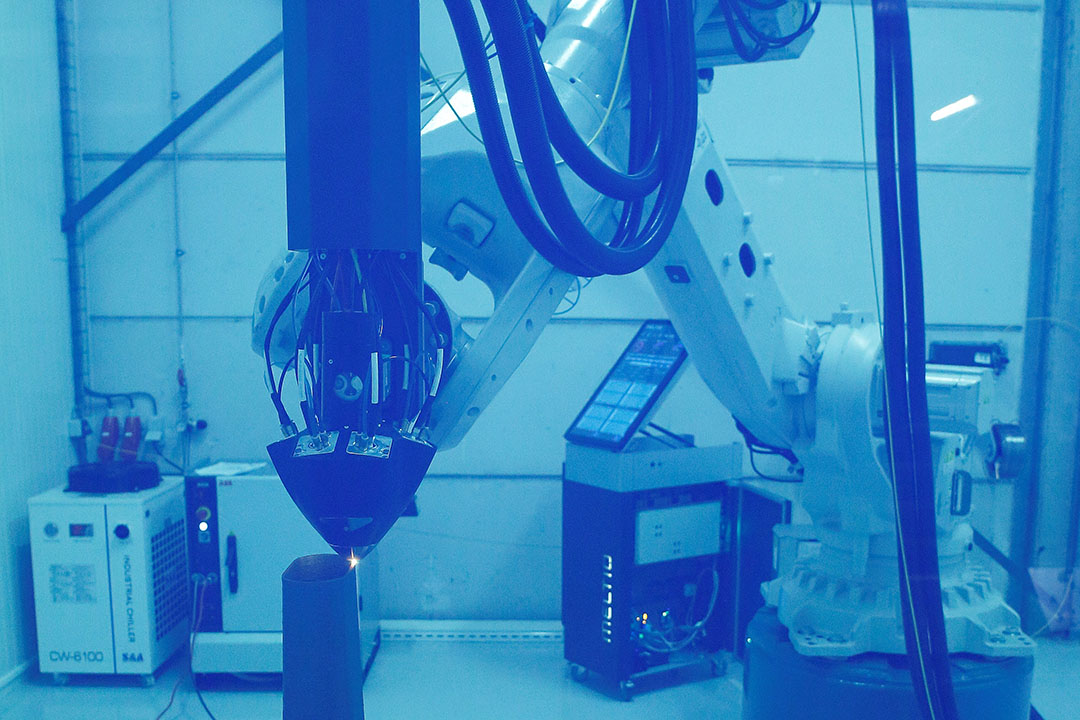
De nieuwste ontwikkeling is 3D-printen met een lasrobot. Die werkt in een afgesloten ruimte, waarbij er een inert gas uit de nozzle van de robotkop komt. Het smeltbad is in principe vrij miniem, maar vereist toch bescherming van de ogen. Vandaar dat de ruimte is afgeschermd met speciaal glas.
Onderdelen produceren tegen lagere prijs
De 3D-printtechniek maakt het mogelijk onderdelen tegen een relatief lage prijs te produceren. De prijs hangt hoofdzakelijk af van de afmeting en het volume van het onderdeel. Dat kan iets zijn dat nergens meer te koop is. Of het onderdeel is slechts in kleine aantallen nodig, waardoor bestaande technieken als (spuit-)gieten of stansen te duur zijn. Matrijzen, gietvormen of stempels maken is prijzig en alleen interessant voor grote aantallen.
Een bekend voorbeeld zijn onderdelen die met spuitgiettechniek worden geproduceerd: vloeibare kunststof of metaal dat onder hoge druk een stalen matrijs ingaat. Binnen enkele seconden verhardt het materiaal, de matrijs gaat open en het onderdeel valt eruit. Denk aan stopcontacten, plastic flessen of schakelaars, maar ook aan de behuizing van een hogedrukpomp.
Bijna elke vorm te 3D-printen
3D-printen maakt het ook mogelijk onderdelen te produceren die je met bestaande technieken niet kunt vervaardigen. De ontwerper moet een gietvorm namelijk zo maken dat het onderdeel los kan komen uit de mal. Bij 3D-printen is die beperking er niet. Bijna iedere vorm is te printen, zelfs scharnierende constructies.
Een bijzonder voorbeeld dat de specialisten in Terborg laten zien is een mesje voor de broodbakindustrie om een sneetje in het deeg te maken. Ze kunnen een holle ruimte voor luchtaanvoer in de steel van het mesje printen en het mesje poreus maken, zodat er tijdens het snijden lucht uit stroomt die het mesje schoon houdt. Met conventionele technieken is zoiets vrijwel onmogelijk te maken. Met 3D-printen is het eenvoudig om het ontwerp nog aan te passen, maar ook om er bijvoorbeeld een naam of een logo in te printen. Dat kan per stuk worden gewijzigd.
Tekst gaat verder onder de foto
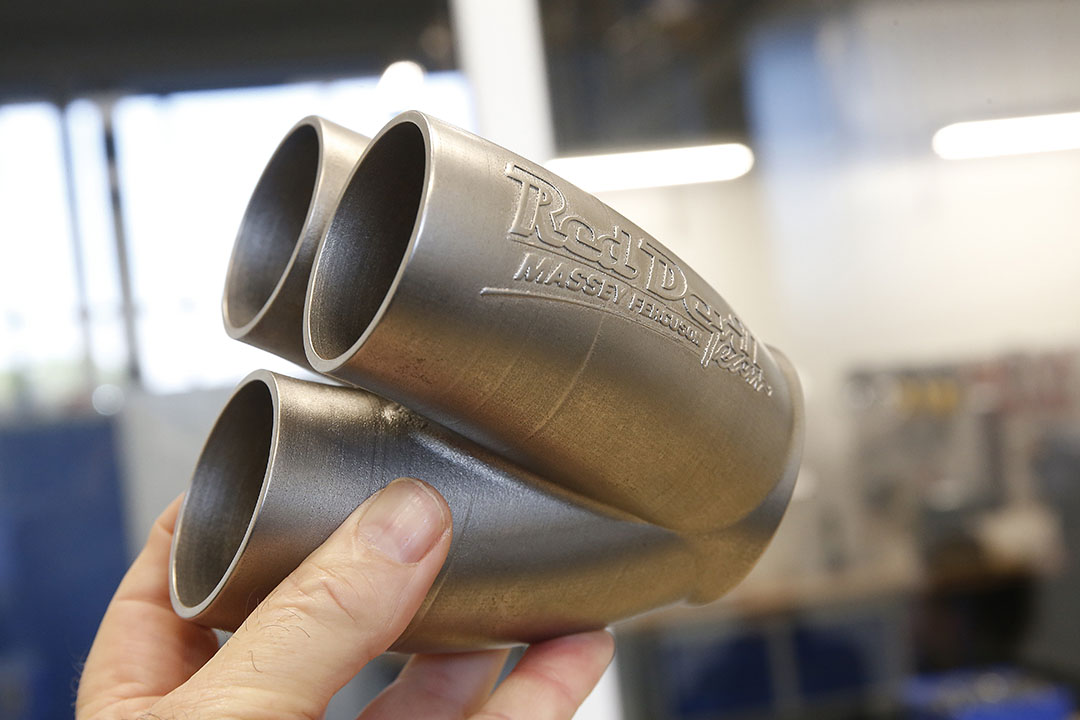
Met de hand lastig te maken, maar voor de 3D-printer een eenvoudige opdracht: een spruitstuk voor de motor van de Red Devil, inclusief naam en logo.
Beperkingen en mogelijkheden 3D-printer
Een beperking van 3D-printers is de geringe capaciteit. Afhankelijk van het formaat onderdeel staat een metaalprinter al gauw een of twee dagen te stampen. Soms zelfs aanzienlijk langer. De bodemplaat van de printers bij K3D meet 42 bij 42 centimeter. Dat is het theoretische maximum van de afmetingen van het onderdeel. De maximale hoogte is 40 centimeter. Om de capaciteit te optimaliseren, printen de medewerkers vaak meerdere onderdelen gelijktijdig, of gesorteerd op printhoogte.
Het oppervlak houdt door het printen altijd een zekere ruwheid. Vaak worden onderdelen gepolijst door te stralen of te trommelen. Maar omdat K3D hoogwaardig metaal print, kan dat ook thermisch worden gehard. Indien nodig kan het bedrijf bijvoorbeeld pasvlakken achteraf nog polijsten, slijpen of afdraaien. Tot een diameter van 9 millimeter print de machine ook schroefdraad. Ook die kun je met een tap nog extra zuiver maken.
Tekst gaat verder onder de foto
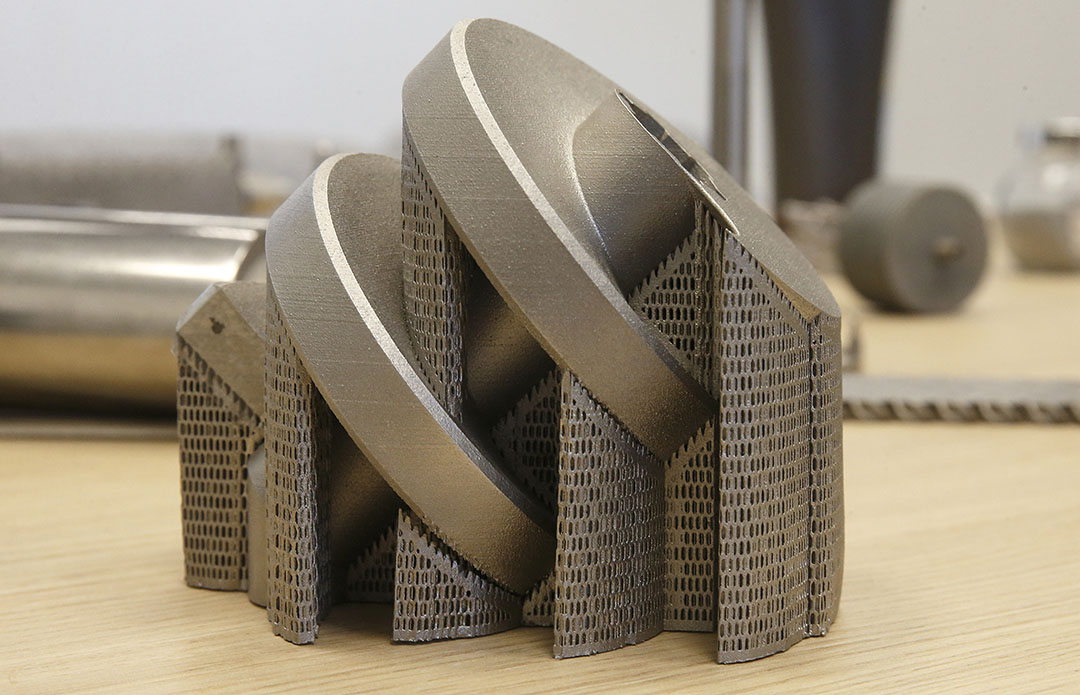
Zo print je een spiraal. Zwevend in de lucht printen gaat niet, daarom wordt een brosse structuur als steun meegeprint. Die is later vrij eenvoudig te verwijderen.
Wat kost een 3D geprint onderdeel?
Het begint met een goede 3D-tekening. K3D werkt het liefst met een zogenoemde STEP-file. Het bedrijf heeft de kennis in huis om deze zelf te maken en te vertalen naar instructies voor de printer. Een alternatief is het inscannen van een bestaand onderdeel. Ter indicatie: een deurklink van een auto scannen en printen komt op een paar honderd euro.
De hoeveelheid benodigd materiaal is sterk bepalend voor de prijs, omdat deze de printtijd bepaald. Zeg ruwweg € 500 tot € 1.500 per geprinte kilo voor RVS 316L. Titanium is verreweg het duurste materiaal om mee te werken.
De levertijd van het onderdeel is vanaf tien dagen na akkoord voor de opdracht, met een maximum van drie tot vier weken.
Auteur: Martin Smits
Gerelateerde tags: 3D-printen